Understanding Particles and Their Impact to Biologics and Biosimilars
Particles in an injectable drug product represent a huge risk not only to patient safety – but also to a drug company’s reputation and bottom line. Presence of visible or sub-visible particles has been one of the most common reasons for recalls. According to the FDA Recalls, Market Withdrawals, & Safety Alerts database, 23 of 59 (39%) recalls, market withdrawals, and safety alerts between 2018 and 2020 were due to particulate contamination1.
![]()
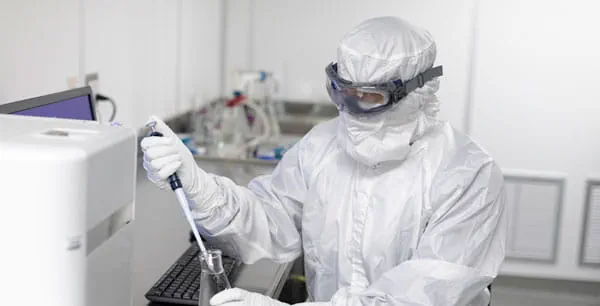
The presence of particles in an injectable drug product is regulated in the harmonized pharmacopeial chapters USP <788>, Ph.Eur. 2.9.19, and JP 6.07. In the case of biologics and biosimilars, USP <787> is also applicable. USP <787> allows for the analysis of smaller volumes of drug product. The limits set forth in <788> must be met and particles from 2 µm to 10µm must be monitored and trended. USP <787> and guidance chapter <1787> introduce the concept of inherent particles, adding to the concepts of extrinsic and intrinsic particles that are described in guidance chapter <1788>.
- Inherent particles are related to the product itself and represent a potentially acceptable characteristic of the product.
- Extrinsic particles are foreign to the manufacturing (formulation, packaging, and assembly) process. They consist of materials such as fibers, cellulosic matter, vegetative matter, and corrosion products.
- Intrinsic particles are associated with the packaging, product formulation, assembly process, or formulation ingredients.
Particles must be controlled; they can cause a variety of concerns such as capillary occlusion, pulmonary granulomas, and phlebitis2. Moreover, the presence of extrinsic particles represents a possible loss of process control and may have implications on sterility.
Inherent particles may be present in acceptable levels, but it is important to monitor and trend them. They are subject to self-association6 and degradation during product storage3. For example, protein aggregation can occur due to interaction with intrinsic particles, such as silicone oil4, that are present in the drug formulation7. Another example, inherent particles in the sub-micron range present during product manufacture may shift over time to the sub-visible range.
Particle classification is necessary to perform risk-based evaluations and implement a product life-cycle approach. Therefore, it is critical to use detection technology that is capable of characterizing or identifying particles5. This is especially the case for biologics and biosimilars in which inherent particles must be differentiated from the remainder of particles. In addition, biosimilars may show only minor differences to the innovator product, meaning the particle profiles may be different. Therefore, it is important that particles are clearly identified in order to understand potential impact at each stage of the process. A stability program should be established so that out-of-trend or atypical results can be investigated to determine if inherent sub-visible particles are forming due to agglomeration.
West Analytical Services supports particle testing of biologics and biosimilars, from compatibility testing through product stability. West has the capability to perform sub-visible particle analysis using light obscuration (LO) and characterization of said particles using dynamic image analysis (DIA). With DIA, it is possible to differentiate intrinsic particles (such as silicone oil) from extrinsic particles (such as fibers from inherent protein-related particles). West capabilities also include Raman, micro FT-IR, and SEM/EDS capabilities, for the identification of sub-visible and visible particles.
West partners with customers to design and execute robust, ISO- and USP-based studies, that meet needs and enable an intimate understanding of particle sources related to packaging and delivery systems. For more information on our Analytical Service capabilities click here or contact our Technical Customer Service team.