USP <382>: Think Systems; Not Components Part 4 - Packaging/Delivery System Integrity and Needle Self-Sealing Capacity of Syringe and Cartridge Systems
USP General Chapter<382> Elastomeric Component Functional Suitability in Parenteral Product Packaging/Delivery Systems is slated to become official on December 1, 2025. This allows five years from the date of publication in December of 2020 for stakeholders to implement the new testing requirements for full compliance. While that date seems to be far off in the future, there has been interest in early adoption of the new chapter and implementation of the various tests it requires.
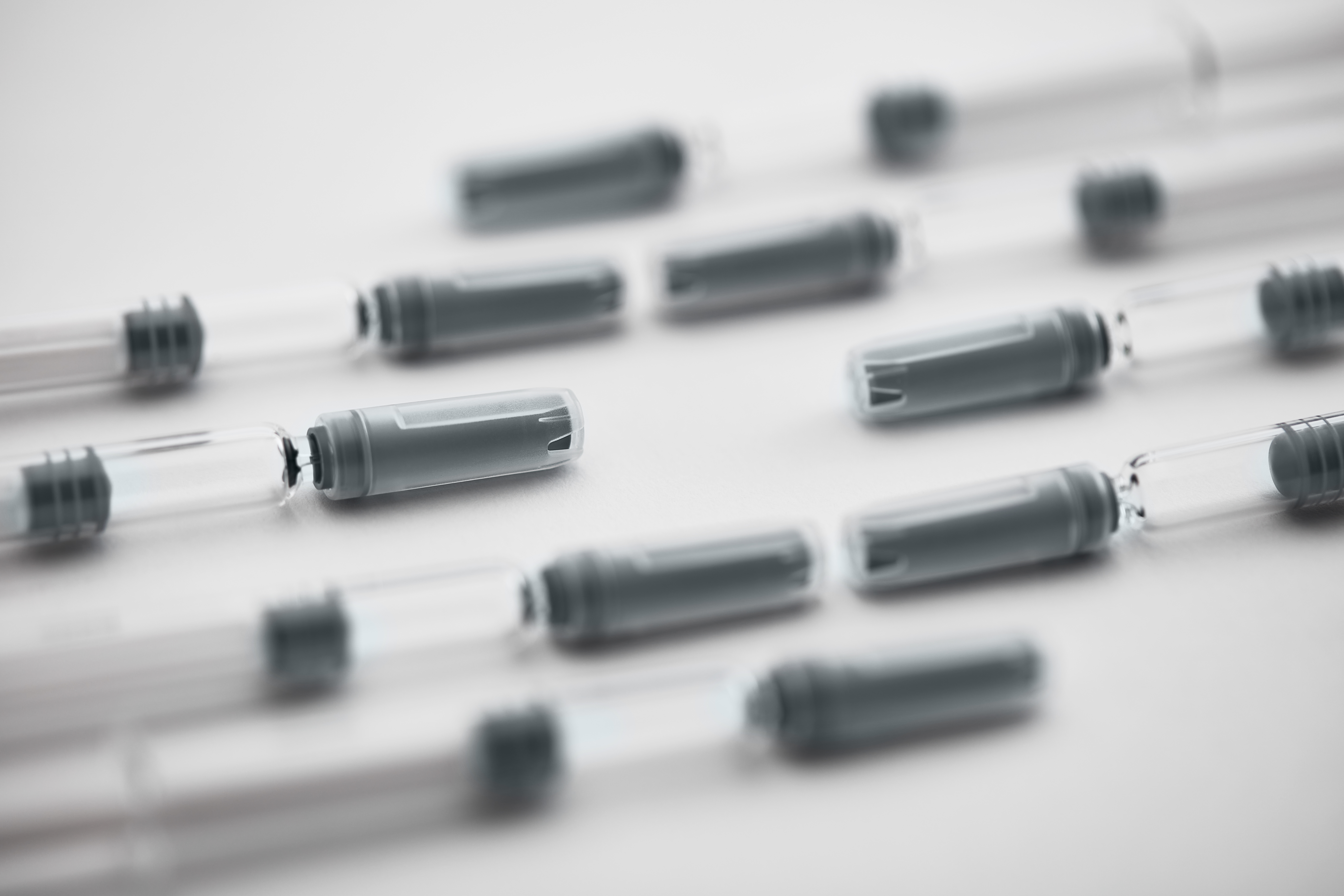
Scope of USP <382>
USP<382> introduces a paradigm shift away from testing elastomeric components individually by the supplier, as was done historically under USP <381>, to a holistic evaluation of these components when assembled into drug product packaging and delivery systems. In addition, the testing is performed on the final package configuration as produced by the manufacturer, using product-filled systems or systems filled with a suitable proxy, where applicable. The scope of the chapter includes an evaluation of both syringe and cartridge systems.
Prefilled syringes are supplied by the drug product manufacturer prefilled with the dose and ready for administration to the patient. These types of packaging systems are sealed with two elastomeric components on either side of the barrel: the plunger (also called the piston), which expels the contents of the syringe, and either a needle shield or a tip cap. Likewise, cartridge systems are also sealed with two elastomeric components on either side of the cartridge: the septum, which is held in place by a seal (also called a cap), and the plunger. Here, the septum allows for product access through penetration by a double-sided needle, while the plunger expels the contents of the cartridge. There are two main types of product use applications for cartridge systems: dental local anesthesia products, and pen injector products used to treat diabetes or growth disease such as pediatric growth hormone deficiency.
USP <382> Testing
West can perform the testing required in USP <382>, including container closure integrity testing, as described in section 4 Packaging/Delivery System Integrity Tests and section 5.3 Needle Self-Sealing Capacity. Both sections of USP <382> refer to USP <1207> Package Integrity Evaluation – Sterile Products and its sub-chapters for guidance on container closure integrity testing. This blog describes the testing required in USP <382> sections 4 and 5.3 and discusses why helium leak detection is an ideal leak test for both evaluations for syringe and cartridge systems. Vial systems were discussed in an earlier blog in this series.
The testing described in USP <382> section 4 Packaging/Delivery System Integrity Tests examines the fit of an elastomeric closure with its container. The resulting packaging/delivery system must protect the therapeutic from product loss and contamination from microorganisms or other environmental contaminants, while preserving product quality, safety, and efficacy. Therefore, packaging/delivery systems must be evaluated for two key attributes:
- inherent container closure integrity, which is “the leakage rate of a well-assembled package/delivery system with no system defects”; and
- the ability of the system to achieve the maximum allowable leakage limit (MALL).
About USP Chapter<1207>
USP<1207> defines the MALL as “the greatest leakage rate (or leak size) tolerable for a given product packaging/delivery system that poses no risk to product safety and has no impact, or inconsequential impact, on product quality.” For the packaging/delivery system integrity test, USP <382> requires that thirty (30) samples of each packaging/delivery system are tested for inherent container closure integrity. The systems are acceptable if the inherent container closure integrity results conform to the MALL established for the specific drug product that is contained in the system. When the sterility of a product must be preserved, USP <1207> indicates that a conservative MALL for drug products contained in rigid packaging is a defect size of approximately 0.2 microns ± 0.1 micron, which correlates with a helium leak rate of approximately 6 x 10-6 std cc/sec or the “Kirsch limit.” Lee Kirsch established the relationship between microbial ingress and helium leak rate in glass vial systems. Kirsch determined that at this leakage rate, the probability of microbial ingress is less than 10%; however, well-sealed syringe and cartridge systems using West components can achieve helium leak rates in the range of 10-8 to 10-9 std cc/sec. It is important to understand the kinds of defects that could result in critical leaks for syringe and cartridge systems (i.e., loose or damaged crimp seals on the cartridge; cracks or chips anywhere on the body of the syringe or cartridge; and stopper and piston defects, such as malformation, mold cavity damage, voids, splits or tears, and trim defects) and to employ a leak test that can reliably detect these leaks.
Testing described in USP <382>
The testing described in USP <382> section 5.3 Needle Self-Sealing Capacity applies to multiple-dose product packaging/delivery systems with closures that are punctured multiple times with a needle. Punctures of the closures may be made during dosage form preparation and subsequently for product access for patient administration. While Needle Self-Sealing Capacity is not applicable to prefilled syringe systems, the closures of cartridge systems are pierced multiple times only for product access for patient administration, as dosage form preparation is not needed. Multi-dose systems must be evaluated for two key attributes:
- in-use system integrity, which is “the ability of the punctured closure to prevent microbial ingress and product loss between and during periods of product access”;
- in-use MALL, which is “the level of protection required that ensures maintenance of product physicochemical and microbiological quality attributes between and during periods of product access.”
USP <382> section 5.3 provides detailed instructions for the preparation of cartridge systems, and states that thirty (30) samples are to be evaluated. Multiple punctures are made in the closure using the designated product access needle to “simulate the most challenging in-use directions.” If the product access needle is not specified, then a 27-gauge needle is recommended for use with dental cartridges, while a 29-gauge needle is recommended for all other types of cartridges. Each closure must be punctured 1.5 times the maximum number of possible penetrations in a manner that is consistent with the intended-use instructions using a new needle for each puncture. The cartridge system is acceptable if the in-use system integrity results for all test samples conform to the in-use MALL demanded of the product to ensure product sterility and quality.
To evaluate in-use system integrity at the in-use MALL for multi-dose cartridge systems, USP <382> again refers to USP <1207> and its sub-chapters for package integrity evaluation, recommending the use of deterministic leak tests rather than the probabilistic dye immersion test previously performed under USP <381> section 4.3.3 Self-Sealing Capacity. When selecting the most appropriate leak test for USP <382> needle self-sealing capacity, one must consider the in-use MALL because the leak test technology must be sensitive enough to detect leaks at or below this limit. Because sterility must be preserved throughout usage, a conservative in-use MALL for rigid multi-dose cartridge systems would be the Kirsch limit.
So which type of leak test is most suitable for packaging/delivery system integrity and needle self-sealing capacity for syringe and cartridge systems? Let’s weigh our options. Leak tests such as high-voltage leak detection (HVLD), vacuum decay, and dye immersion are not sensitive enough to detect leaks down to the MALL because the detection limits for these technologies range between 2-20 microns. Therefore, these techniques are not considered appropriate for demonstrating inherent container closure integrity. Laser-based gas headspace analysis, such as oxygen headspace analysis, is sensitive enough to detect leaks down to a MALL of 0.2 microns, so this leak test is suitable for packaging/delivery system integrity testing.
Helium Leak Detection Test
Helium leak detection is an ideal leak test for both packaging/delivery system integrity and needle self-sealing capacity for syringe and cartridge systems. With this technology, an ultra-high vacuum is applied to either end of the empty syringe or cartridge system to force helium tracer gas through any leak path that may be present at either seal end of the syringe or cartridge system into a mass spectrometer for detection and leak rate quantitation. The mass spectrometer is tuned to the mass of helium, making detection specific to only helium tracer gas. Helium leak detection is deterministic and sensitive down to and below the Kirsch limit, with a quantitation limit of 10-9 std cc/sec. This quantitation limit is 1,000-fold more sensitive than the Kirsch limit. In addition, helium leak detection generates quantitative helium leak rate results within a 60-second test cycle due to the application of the ultra-high vacuum.
Information specific to the mechanical testing requirements for syringe and cartridge systems is detailed in the blog titled USP <382>: Think Systems, Not Components Part 3; Fragmentation, Plunger and Tip-Cap/Needle-Shield Functional Suitability. Learn more on container closure integrity testing or refer to West’s Knowledge Center for a comprehensive library of supporting information regarding West’s products and services. Contact us for more information on partnering with West for your USP <382> testing needs.