Emergence of Plastic Caps
Many injectable drug products, such as monoclonal antibodies and recombinant proteins, are susceptible to degradation over time when stored at ambient temperature. As such, they are stored, and subsequently delivered, in a lyophilized state - which enables a much longer shelf life. Lyophilization (also known as freeze-drying) is a process by which all water is removed from a drug product. Absent water, all metabolic processes stop, and drug products thus stored in a lyophilized condition are far more stable. At the time of use, the lyophilized drug product is reconstituted with water (or other appropriate solution) and delivered to the patient.
![]()
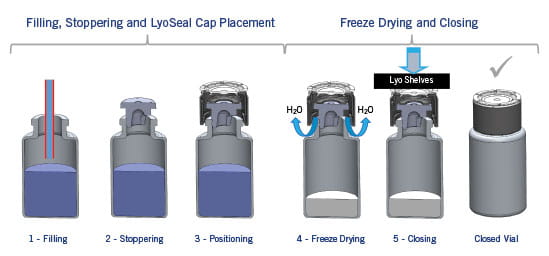
The process of lyophilization involves placing drug product (in a vial, with a partly inserted lyophilization stopper) in a vacuum chamber and decreasing the temperature below the freezing point of water. After drug product is frozen, a vacuum is applied. Under these conditions, water sublimates (i.e., goes directly from solid to vapor) and leaves the drug product - escaping through the vent in the lyophilization stopper. The entire process typically takes on the order of 24 hours. Of course, the exact conditions and time vary depending upon the drug product. After lyophilization, trays in the vacuum chamber are lowered to fully insert lyophilization stoppers.
Typically, the now-closed vial/stopper system is removed, and an aluminum seal applied by crimping to hold the stopper in position. This step presents issues: (a) systems are brought into a possibly nonsterile environment before crimping/sealing - a risk to patient safety, (b) the possibility exists that a stopper may be dislodged during handling and the system loses sterility before crimping/sealing - a risk to patient safety, and (c) since crimping is an extra unit operation, that also requires manufacturing space - costs are increased.
A solution to these issues, that also minimizes human intervention, is immediate capping within the vacuum chamber with a polymer-based seal such as e.g. West´s LyoSeal® caps. After drug product is placed into vial and lyophilization stopper partly inserted, the cap is placed over the stopper as shown in the figure. Upon completion of the lyophilization process, lowering of trays in the vacuum chamber completes insertion of stopper and the seal “snaps on” on – holding the stopper in place. A fully-sealed system is thus removed from the sterile vacuum chamber. Since seals are polymer-based (e.g. polypropylene), and have a low surface energy, risk of sticking to lowered trays is minimized.
In addition to the seal, proper consideration must be given to the vial and stopper - to ensure that, combined, they meet the maximum allowable leak limit (MALL) for the lyophilized drug product:
Vial: glass or polymer – must be compatible with drug product, and not permit unacceptable level of water permeation
Stopper: elastomer composition (or drug–facing fluoropolymer film), must be compatible with drug product, and not permit unacceptable level of water permeation.
It is expected that the future will see plastic caps become the standard in aseptically manufactured drugs – as they make the process potentially safer, and lower cost. Therefore the complementary West offering including LyoSeal caps for lyophilized drugs and nested DAIKYO PLASCAP® closures for liquid pharmaceuticals covers a wide spectrum of industry expectations.
LyoSeal® is a registered trademark of West Pharmaceutical Services Deutschland GmbH.
PLASCAP® is a registered trademark of Daikyo Seiko, Ltd.