Modern Drugs Deserve Modern Packaging
Moore’s Law states that the number of transistors in a circuit doubles approximately every two years. This once lofty prediction proved accurate and has been the basis for long-term planning, not just for the semiconductor industry, but research and development in general.
![]()
Much like semiconductor circuits, advancements in scientific discoveries in the pharmaceutical industry have paved the way for explosive growth in biologic drug development. Pharmaceutical drug products, specifically biologics, are not a new concept. However the advancement of monoclonal antibodies and protein therapies are prompting manufacturers to examine the impact of packaging material selection in product development. With this knowledge in hand, manufacturers are thinking more about the significance of the entire container closure system and the important role it plays in delivering effective therapies to patients.
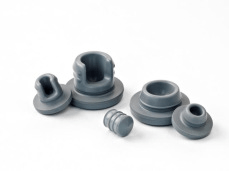
Pharmaceutical packaging and regulatory changes are responding to the rapid growth of biologics in the marketplace. A clear path of communication between the innovator and the packaging industry needs to be established to ensure the appropriate components are recommended. Biologic drugs are more sensitive to extractables, particulate, etc., which may alter the active pharmaceutical ingredient (API) of the drug. Thus, packagers must consider how container closure systems, and the materials used in their construction, can impact the quality of the biologic products they hold.
Change…adapt…adjust. All are synonymous with being reactive. Any advancement in the pharmaceutical industry triggers a cascading response for packaging, governance, and all other industries directly linked to a drug. If testing methods and legacy packaging standards are “grandfathered” without considering more modern, innovative standards for each product or delivery system, this could be problematic. So how can we reverse the trend of being reactive to becoming more proactive?
West’s NovaPure® product line has been designed using Quality by Design (QbD) principles to help maintain drug purity and efficacy and mitigate risk to the patient. High-value NovaPure components use our most modern elastomeric formulations with Flurotec® barrier film to minimize compatibility issues with drug products. To learn more about the proactive strides West is making in the packaging industry, contact Technical Customer Support.
NovaPure® is a registered trademark of West Pharmaceutical Services, Inc., in the United States and other jurisdictions.
FluroTec® technology is licensed from Daikyo Seiko, Ltd.